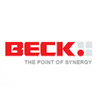
Karakteristike IPC@CHIP-a
Jedan od faktora koji je odlučio da se NT-300 bazira na kontroleru SC143 bila je i brzina koja je potrebna za razvoj. Firma „BECK“ za svoje proizvode iz IPC@CHIP familije embedded kontrolera daje svoj operativni sistem, razvojne kartice za harvder, kao i razvojno okruženje za softver, zajedno sa odgovarajućim primerima.
U ovom slučaju nema potrebe za prilagođavanje operativnog sistema hardveru, kao što je slučaj sa klasičnim kontrolerima, pošto se IPC@CHIP isporučuje sa OS koji je već integrisan u njega. Time se vreme i sredstva uložena u razvoj znatno smanjuju. Prema proceni stručnjaka, prosečno vreme za razvoj proizvoda na bazi ovih kontrolera je od 9 do 12 meseci. Prosečno vreme razvoja istih uređaja koji se baziraju na standardnim kontrolerima je od 15 do 24 meseca.
Arhitektura kontrolera SC143
Da bismo shvatili mogućnosti kontrolera SC143, moramo da se upoznamo sa njegovom arhitekturom. Jezgro kontrolera čini procesor 80186-EX koji radi na 96 MHz. SC143 poseduje hardver koji omogućava RS-232, RS-422, RS-485, CAN, USB i Ethernet komunikaciju, čime se podržavaju asnihroni (CAN, USB, TCP/IP) i sinhroni komunikacioni protokoli (SPI , I²C).
Od posebnog interesa prilikom razvoja bio deo kontrolera koji se zove Chip-Select Unit, jer NT-300 preko njega može da selektuje odgovarajuće periferije, koje su kod nas digitalne i/ili analogne kartice.
IPC@CHIP SC143 poseduje 8MB RAM, i 8MB FLASН memorije. FLASН memorija služi za skladištenje operativnog sistema koji je predviđen za rad u realnom vremenu (Real Time Operating System). U memoriji se nalazi i Bootloader program, koji se prilikom pokretanja kontrolera prvi startuje. Njegov zadatak je da izvrši download RTOS-a u slučaju da na nekom od komunikacionih kanala postoji takav zahtev; u suprotnom će se pokrenuti operativni sistem koji se već nalazi u kontroleru.
U FLASН se smešta i sistem za rad u realnom vremenu (Run Time System) koji omogućava izvršavanje programske logike PLC-a, koja se takođe smeštaju u ovu memoriju.
Programska logika se piše u CoDeSys okruženju koji je predviđen za programiranje prema IEC 61131-3 standardu. Promenljive koje su značajne za naš program (retain) mogu se zapisivati u FLASH. Ova opcija daje PLC-u mogućnost da, u slučaju nestanka napajanja može da zapamti postojeće vrednosti, a time i trenutno stanje sistema za potrebe analize, ili mogućeg nastavka rada od stanja u kom se sistem nalazio (ako se desio kratkotrajni nestanak napajanja).
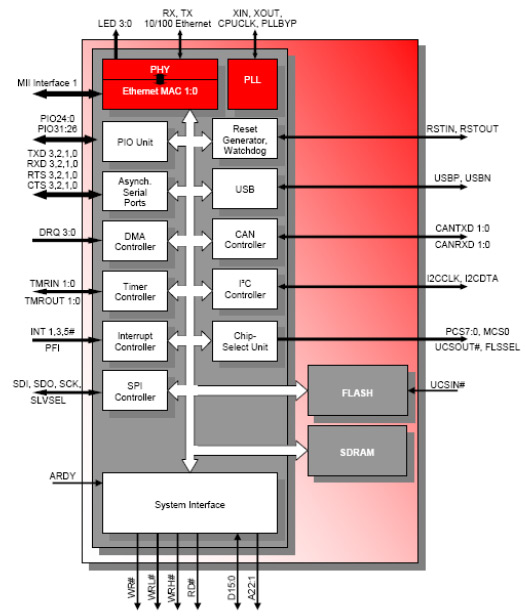
Slika 1. Blok šema kontrolera SC143.
RAM (Random-access memory) memorija ima istu brzinu pisanja kao i FLASH memorija, ali je brža kad je u pitanju upis. Zato se ona koristi kao radnja memorija u kojoj se, radi bržeg izvršavanja, smeštaju aplikacije iz FLASH memorije. Ima neograničen broj upisa za razliku od FLASH-a koji ima mogućnost do 100.000 zapisa.
Mana ove memorije je nemogućnost pamćenja sadržaja prilikom nestanka napajanja. Ovaj problem se može rešiti postavljanje pomoćnog napajanja koje će suspendovati rad kontrolera, ali će obezbediti dovoljan naponski nivo da se sačuva sadržaj RAM-a.
Razvojno okruženje DK61
Razvojno okruženje DK61 je proizvod firme „BECK“, namenjeno za proučavanje mogućnosti i performansi kontrolera SC143. U IPC@CHIP kontroler je integrisan @CHIP-RTOS operativni sistem koji je sposoban za konkuretno izvršavanje do 12 DOS aplikacija. Svaki od programa se izvršava kao jedan od zadataka kernel RTOS-a.
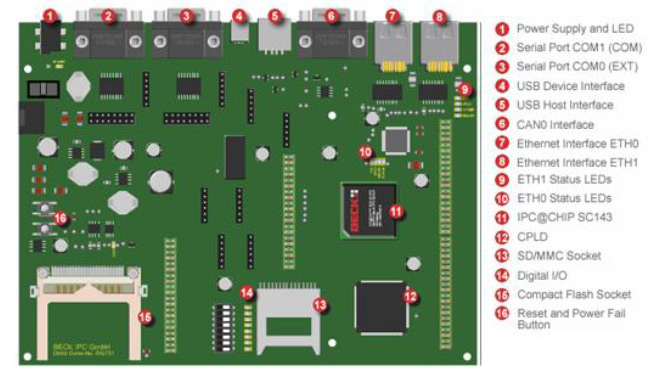
Slika 2. Razvojna elektronska kartica DK60.
Slika 2. daje pregled najvažnijih komponenti razvojne ploče DK60 koja se dobija sa razvojni okruženjem. Pored hardverske komponente, uz ovaj komplet dobija se i softverska podrška, potrebna za programiranje i komuniciranje sa IPC@CHIP-ом. Softverski paket razvojnog okruženja obuhvata:
- IEC Platform Builder
- Paradigm C++ Beck IPC Edition
- @CHIPTOOL
Navedeni programi nam služe za prilagođavanje runtime sistema (RTS-a) našim potrebama.
Koncept IEC Platform-e
CoDeSys je hardverski nezavisno programsko okruženje za programiranje prema IEC 61131-3 standardu, koje može da se prilagodi tj. adaptira bilo kom industrijkom kontroleru. Adaptacija CoDeSys-a znači stvoriti skup softvera koji opisuje i rukuje hardverom kontrolera.
Skup softvera koji prilagođava CoDeSys okruženje specifičnom IPC@CHIP hardveru naziva se IEC Platform-а. „BECK“ je ponudio razvojni alat za kreiranje IEC platforme koji odgovara specifičnostima njegovih IPC@CHIP kontrolera. Proizvođač nudi gotove platforme za DK61, koje služe za razvoj i evaluaciju softvera; tako da je u razvojnom okruženju moguće odmah programirati prema IEC 61131-3 standardu. Pored već dostupnih, nudi se i opcija kreiranja sopstvenih IEC platformi.
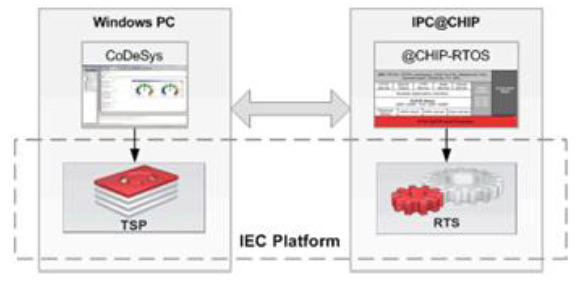
Slika 3. Koncept IEC platforme.
Platforma se sastoji iz dve komponente:
- TSP (Target Support Package). TSP je kolekcija fajlova koja opcisuje hardver Target Systema-a u CoDeSys okruženju. On se instalira na PC, i predstavlja Target koji se bira prilikom kreiranja novog CoDeSys programa. U našem slučaju Target System predstavlja konfiguraciju NT-300.
- RTS (Run Time System). RTS је aplikacija koja radi na @CHIP-RTOS оperativnom sistemu u SC143 kontroleru. Preko runtime sistema se vrši komunikacija između IPC@CHIP-а i CoDeSys programskog okruženja koje se izvršava na Windows-u. Važnija funkcija RTS-а је prihvatanje aplikacija kreiranih od strane CoDeSys-а, i omogućavanje njihovog izvršavanja na IPC@CHIP hardveru.
Komunikacija preko OPC specifikacije
OPC specifikacija je međunarodno prihvaćena serija standarda koji se bave komunikacijom između različitih uređaja u automaticiji. Ona je rezultat saradnje više više svetskih proizvođača koji su sarađivali sa Microsoft-оm. Prvi od standarda koji je nastao zbog potrebe standardizacije je Data Access Specification koji se bazira na Microsoft-оvim OLE COM i DCOM tehnologijama.
Specifikacija je definisala standardni skup objekata, interfejsa i metoda za upotrebu u procesnoj industriji i proizvodnoj automatici. Na ovaj način se ostvarila međusoba kompaktibilnost uređaja. Taj princip je dobio širu upotrebu, i danas postoje stotine proizvođača OPC Data Access servera i klijenata.
Komunikaciju prema OPC specifikaciji smo realizovali korišćenjem CoDeSys komponenti (OPC i Gateway Server) zbog postojanja više SCADA aplikacija koji komuniciraju sa PLC-om, jer su potrebna minimalna podešavanja na OPC serveru, dok se SCADA ne mora reprogramirati.
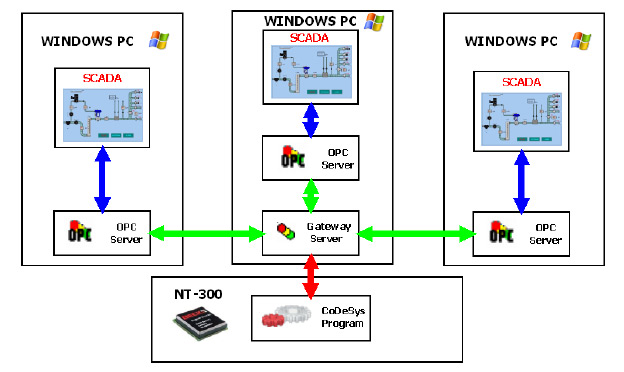
Slika 4. Šema rada OPC-a preko CoDeSys komponenti.
Verzije PLC-a tipa NT-300
PLC-ovi tipa NT-300 su modularni, i isporučuju se u dve osnovne verzije:
- SmallPLC. Verzija je predviđena za automatizaciju malih i srednjih postrojenja. Glavni deo predstavlja CPU kartica koja se bazira na SC143 kontroleru. Kapaciteti kartica za ovu verziju su: analogni ouput (16 izlaza), analogni ouput (16 ulaza), digitalni output (32 izlaza), digitalni input (32 ulaza).
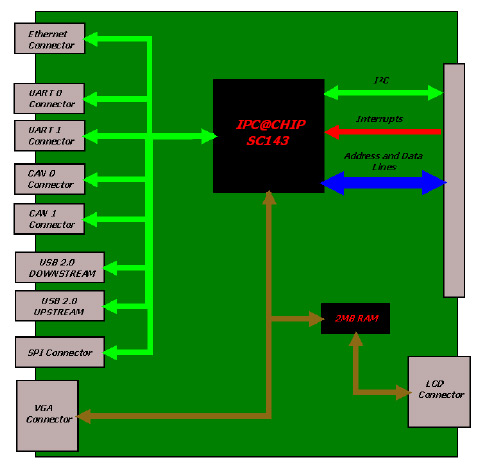
Slika 5. CPU kartica za SmallPLC verziju.
- BigPLC. Ova verzija je predviđena za automatizaciju velikih sistema. CPU kartica se sastoji iz dva dela, tačnije dve kartice koje su u stanju da funkcionišu nezavisno: CPU kartice za SmallPLC verziju. Kartice koja na sebi ima PC modul sa AMD LX-800@0.9W čipom koja omogućava kontrolu i nadzor u samom postrojenju korišćenjem SCADA aplikacije. Kapaciteti kartica za ovu verziju su: analogni ouput (32 izlaza), analogni ouput (32 ulaza), digitalni output (64 izlaza), digitalni input (64 ulaza).
Konfiguracija BigPLC-a može maksimalno da ima 1280 digitalnih ulaza/izlaza, odnosno 640 analogni ulaza/izlaza. Važno je da napomenuti da su sve digitalne i analogne kartice radi zaštite galvanski izolovane.
Primer implementacije
PLC tipa NT-300 upotrebljen je za potrebe automatizacije revitalizovanog postrojenja firme „Linde-Gas“ koja se bavi proizvodnjom CO2 (ugljen-dioksida).
Konfiguracija verzije BigPLC, која se trenutno nalazi u postrojenju, sastoji se od: jedne CPU kartice, 3 digitalne input kartice, 2 digitalne output kartice, 3 аnalogne input kartice, 1 аnalogne output kartice. Na osnovu broja kartice može se izračunati da postojeća konfiguracija može makcimalno da ima: 192 digitalna ulaza, 128 digitalna izlaza, 96 analogna ulaza i 32 analogna izlaza.
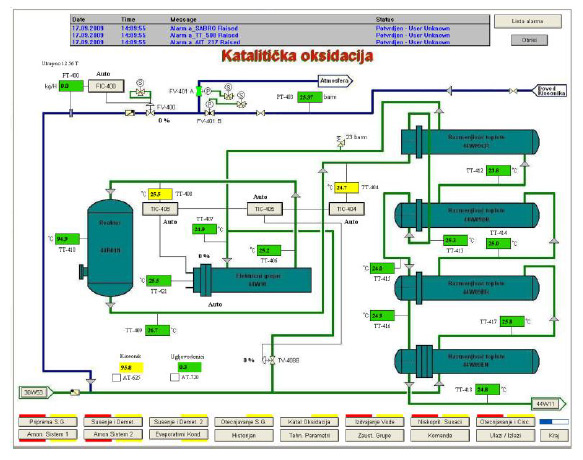
Slika 6. „Katalitička oksidacija“ – SCADA
Za potrebe ovog posla je napravljena SCADA u CX-Supervisor okruženju firme „Omron“ koja se sastoji iz 18 glavnih i 35 pomoćnih formi tj. prozora. U aplikaciji se nalaze i skriptovi u kojima se nalazi programski kod koji vrši preračunavanje veličina iz AD u inženjerske jedinice i obrnuto, kao i registrovanje alarma.
Takođe je omogućena komunikacija sa bazom podataka koja je urađena u Microsoft Access-u i gde se beleže tehnološki parametri i granice značajne za postrojenje. Brzine komunikacija između PLC-a i SCADA aplikacijа nije bila zadovoljavajuća usled velikog broja promenljivih. Zato je izvršena optimizacija na taj način što je jedan deo promenljivih pretvoren u nizove čime nema pojedinačnog slanja, već se vrši slanje blokova podataka. Drugi deo promenljivih se ne osvežava redovno, već se to vrši samo kada se za to ukaže potreba tj. kada operater hoće da ih vidi. Na taj način je smanjen broj promenljivih koje se u trenutku očitavaju sa OPC servera, čime je povećana brzina odziva SCADA.
Zaključak
Iako je u rado pokazano da NT-300 potpuno ispunjava IEC 61131 standard, postoji još mogućnosti za njegovim usavršavanjem. „BECK“ sada nudi novu verziju IEC platforme koja omogućava čitanja, odnostno pisanje i u toku scan ciklusa, a ne samo na njegovom početku i kraju (klasičan PLC). U tom slučaju svaki task CoDeSys programa može da se izvršava samostalno čitanje i pisanje, a da ne mora da čeka početak i/ili kraj cikluca. Ovakvo rešenje povećava brzinu odziva PLC-a.
U budućnosti se planira prilagođavanje NT-300 standardu IEC 61499 koji se odnosti na distribuirane upravljačke sisteme. Firma „ISaGRAF“ je prva napravila softver koji ispunjava ovaj standard, i on je komaktibilan sa SC143 kontrolerom, što znači da se ovaj softver može implementirati u PLC.
Napomena: Učestvovanjem u nagradnoj igri Automatika.rs zadržava pravo objavljivanja teksta i nakon završetka nagradne igre. Takođe ne snosimo troškove eventualno nastale štete zbog krivo objavljenih ili pogrešno napisanih tekstova. Za istinitost tekstova, vlasništvo nad autorskim pravima, na fotografije ili tekstove koji se koriste, a preuzeti su s drugih web stranica odgovara isključivo vlasnik teksta.