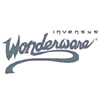
U radu je dato idejno rešenje
SCADA aplikacije za vođenje procesa pneumo-transporta zeolita u fabrici glinice
„Birač“ A.D. Zvornik. U tu svrhu korišćen je softverski paket
Wonderware InTouch. Izvršena je diskusija o mogićim pravcima nadgradnje postojećeg relejnog sistema upravljanja kroz dve SCADA konfiguracije. Odabrano je rešenje koje podrazumeva uvođenje PLC-a pri čemu je predložena komunikaciona veza zasnovana na
TCP/IP protokolu.
Razvijena je aplikacija koja kroz jednostavan sistem signalizacije i alarma pojednostavljuje vođenje procesa i tako povećava funkcionalnost i produktivnost rada.
1. Uvod
U fabrici glinice „Birac“ A.D. Zvornik pneumo-transport zeolita vrši se iz prihvatnog silosa u betonski silos. Zeolit se izuzima iz prihvatnog silosa u pneumo-komore, kojih ima dve i koje rade naizmenicno (jedna se puni a druga prazni i obrnuto). Potrebno je omogućiti da komore mogu raditi autonomno jedna od druge. Iz komora se zeolit transportuje kompriminovanim vazduhom p=2.5 bar kroz cevovod definisanog poprečnog preseka u betonski silos.
Zeolit je po svom hemijskom sastavu natrijum-alumosilikat, (po obliku beli prah), koji se upotrebljava u deterdžentskoj industriji, a može se prerađivati i u molekularna sita (filtere) te za dobijanje čitave lepeze drugih proizvoda bitnih u hemijskoj industriji.
Obzirom na fizičku rasprostranjenost pogona za proizvodnju zeolita i važnost pouzdanog transporta velike količine proizvedenog zeolita u silos, jasna je potreba za automatizacijom ovog procesa i njegovo vođenje iz komandne sale kroz aplikaciju koja je instalirana na računaru. Na ovoj aplikaciji neophodno je izvesti jasnu signalizaciju stanja opreme kao i indikaciju alarmnog stanja kada proces ne zadovoljava nominalne uslove rada. Za rešenje ovog problema, moguca su dva rešenja:
- SCADA (eng. Supervisory Control And Data Acquisition),
- DCS (eng. Distributed Control System).
ISA S5.1 standard definiše DCS kao sistem koji se iako funkcionalno integrisan, sastoji od podsistema koji mogu biti fizički razdvojeni i udaljeni jedan od drugog. DCS je prvobitno razvijen prema potrebama velikih preduzeća i procesnih postrojenja koji su zahtevali znatnu količinu analognog upravljanja.
Osnovne razlike između SCADA sistema i DCS-a su:
- SCADA koristi programabilni logicki kontroler – PLC (Programmable Logic Controller), a DCS koristi udaljene terminalne jedinice – RTU (Remote Terminal Units).
- PLC poseduje veći nivo inteligencije od RTU-a.
- Za razliku od RTU-a, PLC je u mogućnosti da kontroliše stanice bez direkcija od strane mastera.
U ovom radu biće predstavljeno rešenje koje podrazumeva realizaciju SCADA sistema, a diskusija o opravdanosti ovog izbora data je u odeljku 2.3.
2. SCADA sistemi
SCADA sistemi imaju široku primenu u upravljanju i praćenju rada industrijskih postrojenja i opreme ali i u telekomunikacijama, energetici i sistemima upravljanja. SCADA je sistem koji služi za automatizaciju industrijskih procesa, odnosno sistem koji se koristi za prikupljanje podataka sa senzora i instrumenata lociranih na udaljenim stanicama kao i za prenos i prikazivanje tih podataka u centralnoj stanici u svrhu nadzora ili upravljanja. Prikupljeni podaci se obično posmatraju na jednom ili više SCADA računara u centralnoj (eng. master) stanici. SCADA sistem može da prati i upravlja i do stotinama hiljada ulazno-izlaznih vrednosti. Uobičajeni analogni signali koje SCADA sistem nadzire (ili upravlja) su nivoi, temperature, pritisci, protoci fluida ili gasa i brzine motora. Tipični digitalni signali za nadzor (upravljanje) su prekidači nivoa, prekidači pritiska, status generatora, status kontakta releji itd.
Prikupljanje podataka počinje na nivou PLC-a i uključuje očitavanje veličina i statusa. Zatim se podaci koji su potrebni šalju na SCADA sistem, gde se prevode i formatiraju na takav način da operater u komandnoj sali uz pomoc interfejsa može, na osnovu njih, doneti odgovarajuće odluke koje mogu biti potrebne da bi se podesile normalne funkcije rada PLC-a, a samim tim i procesa. Podaci se takođe mogu čuvati u istorijatu, koji je često podržan bazom podataka, radi prikaza trendova i drugih analitičkih radnji. SCADA sistem tipično implementira distribuiranu bazu podataka, koja se često zove i baza tagova, koja se sastoji od elemenata zvanih tačke ili tagovi. Tag predstavlja jednu ulaznu ili izlaznu vrednost koja se prati ili kojom se upravlja od strane sistema. Tagovi mogu biti tvrdi (eng. hard) ili meki (eng. soft). Tvrdi tag predstavlja stvarnu vrednost ulaznog ili izlaznog signala, dok je meki tag rezultat logičkih i matematičkih operacija primenjenih na tvrdom tagu. Većina interpretacija konceptualno uklanja ove granice nazivajući tvrde tagove najprostijim slučajem mekog taga. Vrednosti tagova se obično čuvaju kao kombinacija vrednost-vreme; vrednost i vremenski trenutak kada je ta vrednost snimljena ili izračunata. Serija vrednost-vreme kombinacija je istorijat tog taga.
SCADA racunar je obično industrijski PC na kome se izvršava sofisticirani SCADA HMI softver. HMI (Human-Machine Interface – sprega između čoveka i računara) je aparat koji procesne podatke predstavlja operateru i kroz koji operater kontroliše proces. Osnovni interfejs operatera je skup grafičkih ekrana koji prikazuju reprezentaciju opreme koja se posmatra.
Tri komponente SCADA sistema su:
- višestruke udaljene terminalne jedinice–RTU (PLC-ovi),
- glavna stanica (master station) i HMI kompjuter(i),
- komunikaciona infrastruktura.
Termin ,,glavna stanica” se odnosi na servere i na softver za komunikaciju sa opremom, a onda i na HMI softver koji se izvršava na jednom ili više računara u kontrolnoj sobi, ili negde drugde. U manjim SCADA sistemima, glavna stanica može biti samo jedan PC, dok u većim SCADA sistemima, glavna stanica se može sastojati od više servera i distribuiranih softverskih aplikacija. Konfiguracija SCADA sistema je veoma različita i zavisi od prostornog rasporeda tehnološkog procesa, upravljačkog zadatka itd., i kreće se od jednoračunarskog sistema do tzv. WASCAD sistema. Treba imati u vidu da što je mreža složenija to ona sve više dobija karakter informacione a ne upravljačke mreže [3]. U zavisnosti od izabrane konfiguracije bira se i komunikaciona infrastruktura. To podrazumeva izbor signalnih nivoa za prenos podataka sa davaca do PLC-a kao i povezivanje PLC-a sa računarom na kom je instalirana SCADA aplikacija. Prve generacije SCADA sistema podrazumevale su totalnu centralizaciju procesa i korišcenje WAN-a (Wide Area Network). Integracijom LAN-a (Local Area Network) i WAN-a omogućen je početak decentralizacije kroz delenje vođenja procesa na više operatorskih (lokalnih) jedinica. U današnje vreme, a taj trend će se verovatno zadržati i u bliskoj buducnosti, dominira komunikaciona veza zasnovana na TCP/IP protokolu. Iz tog razloga, u ovom radu se predlaže korišcenje ove komunikacije jer ona omogućava kreiranje dispečarskog centra za nadgledanje procesa proizvodnje na nivou kompletne fabrike. Većina savremenih PLC-ova ima instaliran Ethernet modul koji dozovoljava nadgledanje i upravljanje sa velikih udaljenosti uz potpunu bezbednost.
Obzirom na trenutno izvedeno stanje na procesu pneumo transporta zeolita (relejna šema upravljanja), najprikladnije rešenje uvođenja računarskog vođenja procesa je proširivanje postojećeg YOKOGAWA DCS sistema ili uvođenje SCADA sistema (Wonderware InTouch) kao što je to slucaj na objektu Vertikalna peć. Korišćenje YOKOGAWA sistema dozvoljava eliminisanje postojeće relejne realizacije ali neophodna su dodatna ulaganja za nabavljanje ulaznoizlaznih kartica kao i proširivanje (kupovina novih) tagova.
Drugo rešenje, koje podrazumeva uvođenje novog računarskog sistema, na prvi pogled povećava troškove ali nudi i niz prednosti:
- postojeća instalisana oprema (akviziciono upravljačke kartice YOKOGAWA sistema) može se iskoristiti za proširenje kapaciteta proizvodnje zeolita,
- zadržava se realizovana relejna šema upravljanja,
- veća sigurnost jer je smanjena centralizacija (jedan računar vodi celokupan proces i u slučaju kvara istog dolazi do potpunog zaustavljanja svih delova procesa),
- postoji grupa radnika koja je već obučena za rad sa softerskim paketom Wonderware InTouch.
Moguće konfiguracije SCADA sistema za ovu primenu date su u nastavku teksta.
2.1 PC računar sa akvizicionom karticom i davači
Najjednostavnija konfiguracija SCADA sistema svodi se na sistem koji čine sa jedne strane prekidači, davači, releji itd. a sa druge strane PC računar koji preko svoje akvizicionoupravljačke kartice prima podatke, obrađuje ih, formira informacije o kontrolisanom procesu i određuje potrebne upravljačke akcije, ako je to na ovom nivou primene predviđeno. Programska podrška u ovom modelu SCADA sistema svodi se na podršku prihvata signala sa PC magistrala. Akviziciona kartica mora biti osposobljena za prihvat i izdavanje analogih i digitalnih veličina. Ulazne digitalne veličine se uglavnom svode na prihvat signala sa beznaponskih kontakata, a izlazne na relej ili tranzistor relativno male snage. Analogne ulazne veličine se primaju direktno sa mernog davača (eng. transducer), ili iz sklopa koji zajednički čine merni davač i element za prilagođenje (kondicioniranje) signala (eng. transmitter – predajnik) ili iz sklopa koji signal sa mernog davača priprema za direktan prihvat od strane PC računara preko neke od standardnih serijskih komunikacionih veza (eng. tranceiver – primopredajnik). Pod kondicioniranjem signala u ovom slučaju podrazumeva se filtriranje, pojačanje, linearizacija, prigušenje šuma, itd. signala sa mernog davača. Na slici 1. prikazana je šema konfiguracije SCADA sistema koja zadržava relejnu šemu upravljanja.
Za primenu ove konfiguracije nije neophodno uvođenje PLC-a već bi se iskoristila postojeća relejna šema upravljanja a računar bi bio korišćen u svrhu nadzora i izbora načina rada pojedinih komora ili celokupnog sistema. Preko ulazne kartice PC bi dobijao podatke o položaju svih ventila, pritisku i nivou u obe komore. Na osnovu ovih podataka formira se sistem signalizacije i alarma. Preko izlazne kartice šalju se u pogon informacije o izabranom režimu rada (ručni ili automatski) za obe komore kao i upravljački signali za otvaranje ili zatvaranje ventila u rucnom režimu rada.
Slika 1. SCADA sa relejnom šemom upravljanja.
2.2 PC računar i jedan PLC
U jednostavne strukture spada i konfiguracija koja se formira od jednog PLC-a i PC računara sa SCADA aplikacijom (slika 2). Sa ovakvom SCADA konfiguracijom, uvođenje PLC-a bi označilo mogućnost da se sa jednog računara vrši praćenje/upravljanje nekim drugim procesom kao i primenu računara slabijih performansi. PLC bi bio postavljen u pomoćnoj prostoriji komandne sale, kako bi se obezbedili optimalni radni uslovi, i na ulaznom modulu bi primao informacije o pritisku, nivou i položaju ventila. Budući da se projektnim zadatkom (tehnološki zahtevi i mogućnosti) podrazumeva upotreba kontaktnog manometra, vibracionih sondi i ON-OFF ventila moguće je koristiti PLC sa digitalnim ulaznim i izlaznim modulom. Primena ranije pomenute komunikacione infrastrukture zasnovane na TCP/IP protokolu otvara široke mogućnosti primene računara za programiranje i nadgledanje. Softverski zahtevi su Wonderware InTouch i OPC server. Ova dva elementa opisana su u 3. i 4. poglavlju rada, respektivno.
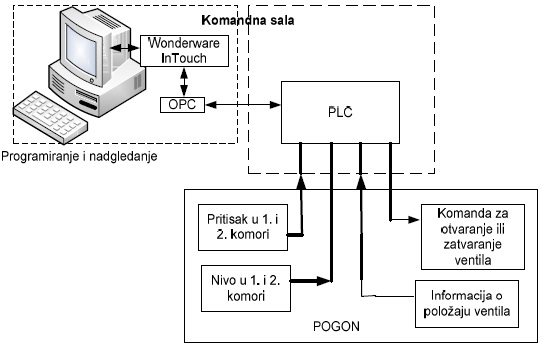
Slika 2. SCADA konfiguracija sa PLC-om.
2.3 Prednosti uvođenja računarskog sistema za upravljanje procesom
SCADA povezana sa automatizovanim procesima omogućava grafički prikaz podataka na ekranu, zajedno sa brojčanim vrednostima, u obliku prilagođenom procesu i operateru. Osim samog prikaza, SCADA omogućava i alarmiranje ukoliko neki od parametara izađe izvan zadanog opsega, ispis i pamćenje svih alarma i merenja na hard disku ili nekom prenosnom medijumu, što otvara mogućnosti za dodatne analize isplativosti i mogućih ušteda u procesu proizvodnje.
Prednosti automatizacije procesa:
- cena – povrat uloženih sredstava u kratkom roku,
- osetno niži troškovi održavanja,
- manji zahvati i troškovi pri revitalizaciji ili rekonstrukciji,
- jednostavno proširenje sastava,
- veca bezbednsot jer se radnici povlace iz potenijalno opasnih radnih uslova,
- brza integracija u postojece sastave:
- baza podataka,
- pracenja resursa i pracenja aktivnosti.
3. Softverski paket WONDERWARE INTOUCH
InTouch je softverski paket razvijen od strane kompanije Wonderware kojim se kreiraju korisničke aplikacije za SCADA sisteme. Za potrebe ovog rada korišćena je verzija 10.0.
Wonderware InTouch se sastoji od tri glavna programska modula, InTouch
- Application Manager-a
- WindowMaker-a
- WindowViewer-a.
InTouch Application Manager organizuje aplikacije koje je korisnik kreirao. Takođe se koristi da bi se konfigurisao WindowViewer kao NT servis ili da bi se konfigurisao NAD (Network Application Development) za klijentski i serverski orijentisane arhitekture ili da bi se podesila konverzija dinamičke rezolucije – DRC (Dynamic Resolution Conversion). DBDump i DBLoad su baze podataka koje se pozivaju iz Application Manager-a.
WindowMaker je razvojno okruženje, gde se objektnoorijentisana grafika koristi za kreiranje animiranih prozora. Ovi prozori mogu biti povezani sa industrijskim ulazno/izlaznim sistemima i/ili sa drugim Microsoft Windows aplikacijama.
WindowViewer se koristi za prikazivanje grafičkih prozora kreiranih u WindowMaker-u. WindowViewer izvršava InTouch QuickScript-e, omogućava evidentiranje i prikaz istorijskog pristupa podacima i izveštavanje, kao i alarme, procese prijavljivanja (tzv. logovanja) i može da funkcioniše kao klijent ili server za DDE i SuiteLink komunikacione protokole.
Pošto je ovim radom predviđeno korišcenje prikaza alarma i trendova, ukratko će biti predstavljeni ovi podisitemi.
3.1 Klijent za alarme
InTouch obezbeđuje korišćenje Alarm Viewer ActiveX Control klijenta za pregled alarma koji je ugrađen u scroll bar. On predstavlja segment kojim se vrši kontrola i pregled alarma. Međutim, InTouch uključuje i mogućnost za distrubuirani prikaz alarma koji unapređuje pregled postojećih alarma bez potrebe da se oni rekonfigurišu da bi se mogli prikazati u Alarm Viewer ActiveX Control-u.
Distribuirani prikaz alarma – Distributed Alarm System (Slika 3.) na jednom ekranu prikazuje i lokalne i daljinski (remote) kreirane alarme. InTouch dozvoljava da se promeni izgled ovog prikaza (uključujući koje će informacije biti prikazane), boje koje se koriste za različita alarmna stanja i alarmne grupe.
Slika 3. Distribuirani prikaz alarma.
3.2 Trendovi u realnom vremenu
Wonderware InTouch dozvoljava dva trenda (praćenje signala) za prikazivanje vrednosti definisanih promenjivih: real-time i historical. Trendovi u realnom vremenu podrazumevaju kreiranje tabela ili grafikona sa 4 podatka (pen), dok istorijski trend dozvoljava 8. Oba trenda se kreiraju pomoću specijalnog alata u WindowMaker-u.
4. OPC
U prošlosti većina kompanija koje su kreirale softver za SCADA aplikacije razvijale su i softver za komunikaciju SCADA aplikacije na računaru sa PLC-om. U današnje vreme je taj problem pojednostavljen jer je razvijen OPC (OLE for Process Control) server.
OPC server je Microsoft Windows aplikacija koja se koristi za razmenu podataka sa PLC-om ili nekim drugim eksternim uređajem i vrši prenos ovih podataka na OPC interfejs. OPC server se obično razvija od strane kompanije koja proizvodi PLC.
OPC klijent je Microsoft Windows aplikacija koja vrši razmenu podataka izmeđ u bilo koje Windows aplikacije i OPC servera. OPC klijent se obično razvija od strane kompanije koja prodaje SCADA softver.
Standardni interfejs za razmenu podataka prikazan je na Slici 4.
Slika 4. Standardni interfejs za razmenu podataka.
Proces razmene podataka je sledeći:
- OPC server inicijalizuje komunikaciju sa PLC-om,
- OPC klijent šalje listu OPC objekata (tagovi) na OPC server,
- OPC server zahteva podatke (čita ih) sa PLC-a i šalje tagove za ažuriranim vrednostima ka klijentu,
- OPC server kontinualno nastavlja da šalje ažurirane podatke (samo onih tagova koji su promenili vrednost) sve dok OPC klijent ne pošalje zahtev za drugim podacima,
- OPC klijent može da pošalje komandu (zahtev) za promenu vrednosti određenog taga. Ovaj zahtev odobrava OPC server i prosleđuje ga ka PLC-u,
- ako se klijent isključi, server će o tome dobiti poruku i zaustaviće i svoj rad.
Organizacija za standardizaciju OPC-a je OPC Foundation.
5. SCADA aplikacija
Prema projektnom zadatku i tehnološkom opisu procesa i tehnološkoj šemi (Slika 5.) pneumo-transporta realizovana je SCADA aplikacija prikazana na Slici 6. Kao što je već pomenuto, u tu svrhu korišćen je softverski paket Wonderware InTouch.
U gornjem levom uglu aplikacije pozicioniran je digitalni časovnik. U gornjem desnom uglu nalazi se trend koji prikazuje vremensku promenu pritiska i nivoa u obe komore. Dodatnim podešavanjem pruža se mogućnost generisanja tabelarnog zapisa ovih promena koja se u obliku tekstualnog dokumenta može čuvati na računaru. U donjem delu prozora nalaze se preklopke za izbor režima rada.
PR1 predstavlja preklopku za izbor režima rada komore 1. Položaj ,,Off” obezbeđuje isključenje napajanja za sve uređaje u sistemu upravljanja tj. ima dvostruku ulogu: isključenje komore 1 iz sistema i hitno isključenje TOTAL STOP prekidac. Položaj ,,Mn” je za ručni režim rada, u kom se svaki ventil može direktno otvoriti pomoću odgovarajućeg prekidača. Ne postoji obaveza slednog uključivanja pojedinih elemenata sistema! Položaj ,,Auto” je za automatski režim rada. PR2 predstavlja preklopku za izbor režima rada komore 2 sa istim karakteristikama kao i PR1. Dodatni uslov za početak automatskog režima rada komore 1 je da je PK1 u položaju “1”. Isto tako, PK2 u položaju “1” za automatski rad komore 2. Za automatski režim rada obe komore, potrebno je preklopke PK1 i PK2 prebaciti u položaj ,,1”. Logika je realizovana tako da se istovremenim uključivanjem komora 1 i 2 u automatski režim rada, prvo puni komora 1. Ako se pusti komora 2 u automatski režim rada a zatim se, pre završetka procesa punjenja, uključi i komora 1 doći će do zaustavljanja procesa punjenja komore 2 i puniće se komora 1. Po završetku punjenja komore 1, nastaviće se punjenje komore 2 pod uslovom da nije promenjen položaj preklopke PK2. Ova blokada postoji samo u slučaju da su obe komore u automatskom režimu rada.
Izbor režima rada za pojedine komore dat je u tabeli 1.
Simbol ,,X” označava bilo koji (neodređeni) položaj PK1 i/ili PK2. Naime, za određenu kombinaciju preklopki PR1 i PR2, položaj preklopki PK1 i PK2 ne utiče na rad sistema.
Predviđen je i prikaz alarma preko koga je moguće dobiti informacije o odstupanju sistema od nominalnih radnih uslova (pritisak u komori iznad max. ili min. dozvoljene vrednosti, određena klapna nije dostigla krajnji položaj usled postojanja prepreke) ali i uspešnom završetku procesa punjenja/pražnjenja, itd.
Signalizacija rada pojedinih elemenata sistema realizovana je jasno i jednostavno, bez nepotrebnog komplikovanja i opterećivanja aplikacije usled čega bi bilo otežano snalaženje operatera.
Tabela 1.
Slika 5. Tehnološka šema pneumo-transporta zeolita.
Slika 6. SCADA aplikacija za vođenje procesa pneumo-transporta zeolita.
5. Zaključak
Sistemi za daljinski nadzor i upravljanje imaju široku primenu u svim granama industrije. U ovom radu predložen je sistem za vođenje pneumo-transporta zeolita u fabrici glinice “Birač” A.D. u Zvorniku. Predlog je da se komunikaciona veza između PLC-a i PC-ja ostvari koristeći TCP/IP protokol i na taj način pruža se mogućnost daljinskog nadzora i upravljanja sa bilo koje lokacije na svetu. Potrebno je samo poznavati IP adresu dodeljenu kontroleru i pravilno podesiti komunikacioni server. Ovde se uočava jedna prednost upotrebe komunikacionih servera jer klijent može biti bilo kog proizvođaca, nezavisno od PLC-a.
Korišćenje TCP/IP protokola će verovatno postati standard u budućnosti jer se dobija sistem visokih performansi koji se može jednostavno nadgledati i upravljati ali i eliminiše se kabliranje koje kod RS-232 veze može predstavljati ograničenje (u pogledu dužine kabla). Na taj način kompletiran je SCADA sistem jednostavan za korišćenje uz punu funkcionalnost svakog njegovog dela.
Naravno da je reč o jednostavnom sistemu koji bi mogao biti baza za razvoj nekog mnogo složenijeg i korisnijeg sistema za daljinski nadzor i upravljanje na nivou jednog objekta pa čak i kompletne fabrike. Osim što bi se mogli ispraviti uočeni nedostaci, takođe bi se moglo razmisliti o uvođenju novih funkcija.
Pravci daljeg razvoja ovog rada idu ka težnji za kreiranje jedinstvenog dispečarskog centra odakle će biti dostupni podaci o stanju svih procesa u fabrici. Budući da savremeni štampači imaju mrežni priključak, mogu se dobiti informacije o svakom procesnom parametru u bilo kom trenutku.
Napomena: Učestvovanjem u nagradnoj igri Automatika.rs zadržava pravo objavljivanja teksta i nakon završetka nagradne igre. Takođe ne snosimo troškove eventualno nastale štete zbog krivo objavljenih ili pogrešno napisanih tekstova. Za istinitost tekstova, vlasništvo nad autorskim pravima, na fotografije ili tekstove koji se koriste, a preuzeti su s drugih web stranica odgovara isključivo vlasnik teksta.