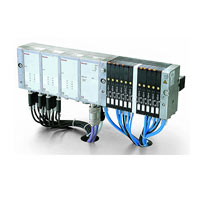
Danas je u upotrebi veliki broj standardizovanih komunikacionih mreža – industrijskih magistrala. Izbor odgovarajućeg standarda zavisi od zahteva konkretne primene, ali i od faktora kao što su dostupnost uređaja koji podržavaju konkretni standard i njihove cene.
Ukoliko napravimo poređenje industrijskih i standardnih računarskih mreža, možemo uvideti da između njih postoje mnoge zajedničke osobine. Računarske mreže omogućavaju komunikaciju između velikog broja računara, a da pri tome računari ne moraju biti direktno, fizički povezani, svaki sa svakim. Svaki računar ima samo jednu vezu sa mrežom. Računarske mreže, takođe, omogućavaju da pojedini uređaji, budu dostupni svim računarima na mreži. Slični ciljevi se postavljaju i pred industrijske mreže, s tom razlikom da sada mrežni čvorovi nisu računari već industrijski I/O uređaji i PLC kontroleri. Pored toga, komunikacioni protokoli koji se primjenjuju u industriji moraju da zadovolje tri osnovna zahteva: bezbednost poruka, pouzdanost rada i maksimalni nivo determinističkog ponašanja.
Razlog prelaska sa analogne na digitalnu komunikacionu tehnologiju
Kod analogne tehnologije su korišćeni su strujni (4-20mA) ili naponski nivoi (±10V). Za povezivanje senzora i aktuatora sa centralnim računarom korišćen je veliki broj paralelno postavljenih kablova. U sistemima sa velikim brojem senzora, aktuatora i drugih uređaja, takvo rešenje je previše komplikovano za projektovanje i montažu, a posebni problemi nastaju pri detekciji i otklanjanju nekog kvara upravo zbog nepreglednosti takvih sistema. Digitalni prenos podataka omogućio je veću preciznost od analognog, što je bio osnovni razlog za razvoj magistrala uređaja. U suštini, industrijske magistrale zamenjuju koncept centralizovanog upravljanja, konceptom distribuiranog upravljanja. Iz tog razloga, industrijske magistrale su mnogo više od proste zamene analognog standarda. Industrijske magistrale doprinose povećanju kvaliteta, smanjenju troškova i povećanju efikasnosti proizvodnje. Sve ove prednosti, u velikoj meri su posledica činjenice da se prenos informacija obavlja u digitalnom obliku.
RS232 je prvi standardni interfejs za serijski prenos podataka. Glavni nedostaci su: malo rastojanje na kome se podaci mogu razmenjivati (do 15m), relativno mala brzina prenosa (do 20 Kb/s) i mogućnost povezivanja samo jednog predajnika i prijemnika. Najznačajniji interfejs za industrijsku primenu u ovoj grupi je svakako RS-485 (poznat i pod nazivima EIA-485 ili TIA/EIA-485). RS-485 je standard koji definiše električne karakteristike interfejsa, i omogućava konfigurisanje jeftinih lokalnih mreža sa multidrop komunikacionim linkovima.
Industrijske magistrale u industrijskim mrežama
Magistrale uređaja su digitalne, bidirekcione, multidrop, serijske komunikacione mreže koje se koriste za povezivanje izolovanih Field uređaja (kontroleri, transduktori, aktuatori i senzori). Za svaki Field uređaj je tipično da poseduje ugrađen mikrokontroler, što ove uređaje čini „pametnim“ uređajima. Pametni uređaji su u mogućnosti da samostalno obavljaju jednostavne funkcije, kao što je dijagnostika, upravljanje i bidirekciona komunikacija. Takođe, u stanju su da automatski izveštavaju o nastalim kvarovima ili o potrebi kalibracije. Ovi uređaji ne samo da omogućavaju pristup sa daljine, već su često sposobni da komuniciraju jedni sa drugima. U oblasti upravljanja senzorima i aktuatorima, kao i akviziciji podataka primenjuje se poseban oblik lokalne mreže – magistrala uređaja ili Fieldbus. Fieldbus se koristi za povezivanje sa decentralizovanim ulazima/izlazima i za vremenski kritičnu komunikaciju između PLC-ova. Pored Fieldbus postoje i mreže zasnovane na CAN protokolu koji čine osnovni CAN i viši CAN protokoli.
Komunikaciona mreža koja se primenjuje u industriji mora da ima odgovarajuće performanse u pogledu iskorišćenosti mreže, propusnog opsega i maksimalnog kašnjenja u prenosu. Performanse i pouzdanost automatizovanih industrijskih sistema u velikoj meri su uslovljeni karakteristikama komunikacione mreže. U mnogim industrijskim postrojenjima prisutni su brojni izvori električnih šumova i smetnji. Uticaj tih smetnji može rezultovati pojavom grešaka u prenosu informacija što može značajno degradirati performanse mreže. Može se reći da je komunikaciona mreža najosjetljivija komponenta automatizovanog industrijskog sistema.
Pri izboru magistrale, najbitniji faktori koje treba uzeti u obzir su: maksimalno dozvoljeno vreme odziva, značaj informacija za bezbedan rad opreme, količina informacija koju treba prenositi, maksimalno rastojanje između umreženih uređaja, namjena uređaja koji se povezuju, mogućnost proširenja i sigurnost.
Dve osnovne kategorije industrijskih komunikacionih mreža su: magistrale uređaja (eng. device bus) i magistrale procesa (eng. process bus).
Magistrale uređaja su optimizovane za razmenu kratkih informacija o statusu i upravljačkih poruka, za razliku od klasičnih računarskih mreža gde propusna moć pri prenosu velikih količina podataka predstavlja ključnu performansu.
Magistrale procesa koriste se za prenos parametara rada kontrolerima procesa koji su u većini slučajeva analogni uređaji. Namenjene su prenosu dužih poruka (paketa), dužine do nekoliko stotina bajtova, što ih čini sporijim, jer su paketi duži. Od većine analognih uređaja ne zahteva se brzi odziv, zato što se koriste za upravljanje procesima koji su po svojoj prirodi spori: protok fluida, koncentracija gasa, temperatura. „Pametni“ (eng. smart) uređaji su oni koji mogu samostalno da obavljaju napredne funkcije upravljanja. Peer nivo se odnosi na mogućnost komunikacije između kontrolera procesa, npr. PLC kontroleri. Zatim slede nivoi ćelije, proizvodnog pogona i nivo celokupne fabrike. Ne postoji magistrala koja pokriva sve nivoe. Razlog za to leži u činjenici da različiti nivoi postavljaju različite zahteve. Pri tome treba znati da magistrala nije samo komunikaciona linija, već i skup pravila, odnosno, protokola, kojih uređaji spregnuti magistralom moraju da se drže.
Najznačajniji FIELDBUS protokoli
Specifični zahtevi korisnika i proizvođača uslovili su da se u prvo vreme na tržištu pojavi više komunikacionih sistema. Da bi se ta delimična konfuzija prevazišla, izvršeno je integrisanje osnovnih karakteristika glavnih komunikacionih tehnika u dva standarda, IEC 61158 i IEC 61784.
Fieldbus tehnologija razvijena je osamdesetih godina prošlog veka sa namerom da se tradicionalno korišćeni prenos analognim signalom (4-20mA i ±10V) zameni sa digitalnom tehnologijom. Osnovni Fieldbus protokoli su Modbus, PROFInet, ProfiBus, Ethernet/IP.
Modbus je serijski protokol koji predstavlja nadgradnju RS-232, sa ciljem njegove primene kao industrijskog komunikacionog protokola. Namijenjen je za povezivanje računara, PLC-ova, operatorskih terminala, senzora, motora i drugih tipova I/O uređaja.
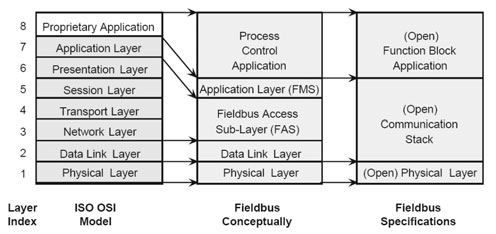
Slika br.1 Poređenje FIELDBUS i OSI modela
Osnovu ovog protokola (nivo 1 i delimično nivo 2 OSI referentnog modela) predstavlja RS-232 kompatibilni serijski interfejs koji definiše parametre poput izlaznih pinova konektora, naponskih nivoa signala, prenosni medijum za prenos poruka, brzinu prenosa, proveru parnosti i slično. Većina Modbus uređaja komunicira preko fizičkog sloja serijskog protokola EIA-485. U sledećoj tabeli prikazane su osnovne uporedne karakteristike protokola koji se koriste u Fieldbus tehnologiji.
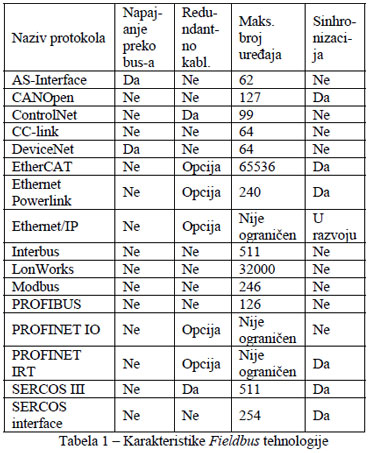
Neka od ograničenja Modbus-a su posledica toga što je on nastao krajem sedamdesetih godina, pa postoji ograničenje broja tipova podataka na one koje su „razumeli“ PLC kontroleri tog vremena. Modbus isključivo tretira master-slave komunikaciju u kojoj jedan od uređaja (master) inicira komunikaciju slanjem upita (eng. query), na šta drugi uređaj (slave) odgovara dostavljajući tražene podatke master-u ili pak preduzimajući akciju koja je zahtevana u upitu.
Ovo znači da uređaj ne može po potrebi poslati podatke master-u, već master mora periodično prikupljati podatke od uređaja u polju i nadgledati promene. Ograničenje takođe predstavlja i maksimalan broj od 246 uređaja na mreži koje mogu biti povezane na master (Tabela 1).
U posljednje vrijeme kao dominantna solucija na tržištu profesionalne opreme u oblasti industrijske i procesne automatizacije izdvaja se ProfiBus. ProfiBus je standardizovan, otvoren komunikacioni sistem za sva područja primene u proizvodnoj i procesnoj industriji. Pogodan je za brze, vremenski zahtevne aplikacije i složene komunikacijske zadatke. Utemeljen je na internacionalnim standardima EN50170 i IEC61158, a u upotrebi je od 1989. godine. Razmena podataka sa distribuiranim uređajima je ciklična, dok se dodatne informacije, kao što su alarmna stanja ili dijagnostički podaci prenose neciklično (na zahtev).
Kada je postalo očigledno da će ProfiBus postati jedan od dominantnih Fieldbus protokola, javila se potreba da se omogući njegova primena u sistemima fabričke i procesne automatizacije koji zahtevaju povišen stepen pouzdanosti i bezbednosti. PROFIsafe je jednokanalni protokol koji se implementira kao nadgradnja na nivo 7 OSI referentnog modela, tako da svi ostali standardni ProfiBus elementi mogu biti nepromenjeni. To je izuzetno povoljno jer ProfiBus može u funkcionisati u redundantnom modu rada ili u koegzistenciji sa drugim uređajima koji poseduju samo osnovnu verziju ProfiBus protokola. PROFIsafe uzima u obzir sve moguće tipove grešaka koje se u procesu serijske komunikacije mogu desiti: vremensko kašnjenje, gubitak podataka, ponavljanje podatka, nekorektna sekvenca bitova u poruci, degradiran kvalitet poruke, pogrešna adresa i slično. PROFIsafe koristi aperiodičnu komunikaciju i može biti korišćen sa RS485, fiber-optičkim ili MBP tehnikama prenosa. Na taj način se istovremeno postiže kratko vrijeme odziva – bitno za primenu u industrijskoj automatizaciji, i inherentna bezbednost rada – bitno u procesnoj automatizaciji.
Kod većih sistema, PLC kontroleri i PC računari komuniciraju međusobno, a i sa IT sistemima unutar kontrolnih soba razmjenjujući velike količine podataka, koji se najčešće prenose kroz neeksplozivnu, bezbednu sredinu, zaštićenu od jakih elektromagnetnih smetnji. Uočavajući da u takvim uslovima i sa takvim komunikacionim zahtevima standardi kao što su TCP/IP, Ethernet i Internet imaju značajne prednosti nad ProfiBus-om, NPO je razvila i standardizovala PROFInet, komunikacioni protokol zasnovan na Ethernet-u koji koristi standardne mehanizme IT komunikacije u realnom vremenu. Pod tim se podrazumijeva upotreba TCP/IP i COM/DCOM (Microsoft Component Object Model i njegovu ekstenziju za distribuirane sisteme – Distributed COM) standarda, trenutno najrasprostranjenijih PC protokola. Prednosti primjene PROFInet-a u odnosu na, recimo, Ethernet se manifestuju tek ako je komunikacija na nižem nivou, nivou distribuiranog sistema ostvarena primenom ProfiBus-a sa kojim je PROFInet maksimalno kompatibilan.
Primena LAN mreža u industrijskom okruženju
Modifikacijom klasičnog Ethernet-a nastao je takozvani industrijski Ethernet koji predstavlja osnovu za realizaciju fabričkih upravljačkih mreža. Industrijski Ethernet (ili Ethernet/IP) pripada grupi mreža koje koriste zajednički industrijski protokol (eng. Common Industrial Protocol – CIP). CIP uključuje sve vrste poruka i servisa za sve aplikacije u automatici, uključujući kontrolu, sigurnost, sinhronizaciju, konfiguraciju i informacije. CIP se može razmatrati kao aplikacioni sloj za DeviceNet, CompoNet, ControlNet i EtherNet/IP. Kao nezavisan protokol, CIP pruža korisnicima jedinstvenu arhitekturu za komunikaciju. Sa nezavisnošću medija dolazi mogućnost da se izabere najbolja CIP mreža za korišćenu aplikaciju. EtherNet/IP omogućava da sa određenim alatima koristimo standardnu Ethernet tehnologiju za industrijske aplikacije. Iako je industrijski Ethernet baziran na istom standardu kao i tradicionalna verzija, implementacija ova dva rešenja nije identična. Osnovna razlika između industrijskog i tradicionalnog Ethernet-a je u tipu hardvera koji koriste. Oprema za industrijski Ethernet je projektovana tako da radi i u grubim industrijskim uslovima. To znači primjenu industrijskih komponenti, specifične metode hlađenja, izlaznu relejnu signalizaciju i slično. Napajanje je standardno industrijsko 24V DC, uz obaveznu primenu i redundantnog izvora napajanja, u cilju povećanja pouzdanosti. Industrijski Ethernet se koristi za komunikaciju između PLC-ova i komunikaciju PLC-ova sa nivoom nadzora.
Na osnovu strukture koju nudi OSI referentni model, može se konstatovati da je tradicionalni Ethernet dominantno lociran na njegovom drugom nivou. Specijalizacija koja je učinjena kod industrijskog Ethernet-a omogućila je da se detaljnije definišu mrežni nivo i transportni nivo OSI referentnog modela. Na mrežnom nivou industrijskog Ethernet-a dominantno se koristi IP protokol. Industrijski Ethernet na transportnom nivou uobičajeno koristi dva protokola: TCP, i ređe korišćen UDP. Na mrežnom i transportnom nivou takođe su implementirane i CIP poruke. Postoje i slučajevi kada se za prenos koristi UDP protokol, umesto TCP protokola (npr. kada je blok podataka koji treba poslati mali, veličine jednog paketa).
Industrijski Ethernet se odlikuje i u specifičnoj realizaciji multicast tipa prenosa. Dok se tradicionalni Ethernet dominantno fokusira na što bolje iskorišćenje raspoloživog propusnog opsega, industrijski Ethernet prioritet stavlja na specifičan zahtev za sinhronizovanim pristupom podacima od strane svih prijemnih čvorova. To je u skladu sa zahtevom za što većim determinizmom u prenosu upravljačkih signala u industrijskom okruženju. Ovaj specifičan zahtev je ispunjen uključivanjem u industrijski Ethernet nekih naprednih funkcija za organizaciju i određivanje prioriteta multicast prenosa. Industrijski Ethernet se često susreće i pod nazivom Switched Ethernet. Ime potiče od činjenice da ovakva Ethernet arhitektura isključivo koristi switch uređaje, a ne hub-ove u implementaciji LAN mreže. Kod industrijskog Ethernet-a se skoro isključivo primjenjuje full-duplex veza. Implementacijom specifične mrežne inteligencije na industrijski Ethernet moguće je realizovati fabričku komunikacionu infrastrukturu koja poseduje fleksibilnost i zaštitu poruka karakterističnih za tradicionalne Fieldbus protokole, uz istovremeno daleko širi propusni opseg, otvorenu arhitekturu i standardizaciju koju nudi Ethernet platforma.
Prednosti koje nudi EtherNet/IP za aplikacije automatizacije u industriji su: kompletna administrativnost(kontrola, konfigurisanje i skupljanje podataka sa „inteligentnih“ uređaja preko jedne mreže), i mogućnost korišćenja jedne mreže kao oslonca za višestruko distribuirane CIP mreže. Kompatibilan je sa standardnim Internet protokolima (HTTP, FTP, SNMP i DHCP), sa standardnim industrijskim protokolima (OPC), kao i sa standardnim industrijskim konektorima.
Interesantna je činjenica da je, upoređujući ProfiBus na 12Mbit/s i Ethernet na 10Mbit/s, prenesena količina podataka u jedinici vremena veća kod Ethernet-a, zahvaljujući protokolima za prenos u većim blokovima.
Specijalne oblasti primene industrijskih komunikacionih magistrala
U mnogobrojnim industrijskim, vojnim, medicinskim, naučnim, ekološkim i drugim primjenama, zahteva se veoma intenzivno i opsežno prikupljanje podataka i informacija iz fizičkog okruženja, za potrebe nadzora i kontrole. Bežične senzorske mreže – WSN (eng. Wireless Sensor Networks) funkcionišu korišćenjem malih, jeftinih i potrošnih platformi koje osim senzorskih funkcija poseduju mogućnost samostalnog formiranja ad-hoc bežičnih mreža u cilju međusobne komunikacije i dostavljanja prikupljenih podataka korisniku mreže. Primena Bluetooth (IEEE 802.15.1) tehnologije predstavljala je korak ka korišćenju adhoc bežičnih mreža u cilju povezivanja i umrežavanja velikog broja uređaja i/ili senzora. Da bi upotreba WSN bila ekonomski isplativa, cena uređaja mora da bude manja od cene uređaja drugih bežičnih tehnologija, npr. Bluetooth. Zahtevi u smislu potrošnje energije, procesorske snage i komunikacionih mogućnosti moraju da se prilagode tehnologijama izrade i ceni raspoloživih rešenja.
U automobilskoj elektronici, kontrolna jedinica motora, senzori, sistemi protiv proklizavanja, i slično, povezani su korišćenjem CAN (eng. Control Area Network) mreže. CAN je serijski komunikacioni protokol koji poseduje veoma visok nivo bezbednosti i podržava distribuirano upravljanje u realnom vremenu. Namenski je razvijen za primenu u motornim vozilima. CAN je protokol zasnovan na porukama i broadcast komunikaciji. Pri tome garantuje integritet podataka u celokupnoj mreži. CAN je multi-master magistrala, što omogućava izgradnju složenih, redundantnih distribuiranih sistema na bazi uređaja različitog nivoa složenosti, a bez potrebe ugradnje centralizovanog, master kontrolera. Osnovne prednosti mreža zasnovanih na CAN protokolu su: niska cena, sposobnost funkcionisanja u različitim okruženjima, podrška radu u realnom vremenu, izuzetno visoka pouzdanost, jednostavna upotreba.
Da bi se ostvarila sinhronizacija svih čvorova na mreži uveden je TTCAN (eng. Time Triggered communication on CAN). To je viši CAN protokol koji obezbeđuje planiranje i realizaciju vremenski determinisanog rasporeda prenosa poruka (eng. Time Triggered – TT). Tako u vozilima tipično imamo TT poruke od sistema za kočenje i ET poruke od sistema za regulaciju temperature. Uvođenje TT poruka je omogućilo implementaciju zatvorenih upravljačkih petlji na sisteme sa CAN baziranim mrežama. Pored TTCAN u više CAN protokole spadaju DeviceNet i CANopen. Pored automobilske industrije, TTCAN nalazi primenu i u domenuindustrijske automatizacije i medicinske opreme, naravno, u daleko manjem obimu.
Zaključak
Tehnološki napredak i pad cena u oblasti komunikacione i računarske opreme doveli su do ubrzanog razvoja i primene računarskih mreža, odnosno, umreženih računarskih sistema.
Industrijski Ethernet se u posljednje vreme sve više koristi u automatizaciji. Pokazalo se da je to mreža koja je najjednostavnija i najisplativija za primenu u postojećim sistemima. S obzirom da Ethernet postaje dominantno rešenje u realizaciji LAN mreža, mnoge industrijske kompanije su počele da ga primjenjuju, u cilju zamene tradicionalnih Fieldbus arhitektura kao što su Modbus, ProfiBus i slično.
CAN magistrala je, zbog svojih dobrih karakteristika i jednostavne ugradnje, našla primenu u mnogim komercijalnim proizvodima, kao i u automatizovanim industrijskim sistemima. Neke od oblasti gdje se može sresti komunikacija zasnovana na CAN protokolu su poljoprivredna mehanizacija, nautička oprema i mašine, medicinska oprema, tekstilna industrija, liftovski sistemi i oprema specijalne namene. Proizvođači medicinske opreme su se odlučili za ovaj protokol jer ispunjava njihove veoma stroge bezbednosne zahtjeve po pitanju pouzdanosti prenosa podataka. Evropska automobilska industrija je prihvatila CAN kao standard.
U oblasti bežičnih senzorskih mreža, dalji razvoj komunikacionih tehnologija, tehnologija izrade senzora malih dimenzija, kao i integrisanih hardversko-softverskih platformi malih dimenzija, potrošnje energije i cijene, omogućava razvoj i primenu bežičnih senzorskih mreža.
Naponema: Dalja objašnjenja pojmova korišćenih u ovom tekstu možete naći u zboniku radova Informacione tehnologije. Autori su: Miloš Perunović, Milovan Radulović, Elektrotehnički fakultet, Podgorica